Insects compete with man every day for their food and shelter. Eliminating pests and pest damage is not an easy job. What man possesses in intelligence, insects and rodents overcome with persistence, reproductive capacity, size and that all-important ability to survive. Stored products are threatened by pests from the time they leave the field to the time they are consumed. Pest management is not about a product, it is about a path of continuous quality improvement to solve pest problems.
Symptom of a Problem.
Problem solvers and pest managers interpret the clues that permit the conditions in which these pests thrive, and eliminate these conditions to discourage these unwanted guests.
In order to reduce customer complaints we always should begin with the insect or other pests first and study what they like and don’t like. Then, we can offer them an environment in which they are uncomfortable and will leave or die.
Companies that put their brand on products are selling more than just the product in the package — they are selling their reputation. Protecting this brand integrity is essential. The expectations of food purity laws and food safety standards are changing. Highly publicized deaths and human suffering from food-borne diseases will force each manufacturer to review its food safety programs and make adjustments. It will force pest managers to be better than ever before.
Peanut butter is used in thousands of brand-name foods. Peanut butter contaminated with Salmonella was traced back to a food processor in Blakely, Ga., as the single source of this outbreak. After all was calculated, more than 1,900 products were recalled and major newspapers in the United States accused the food industry of negligence in protecting the country’s food supply.
As food and grain companies discuss risk management programs, pesticide application has become a sector in which they can lower their risks by out sourcing to qualified, specialized service providers. Service providers like specialized pest management companies, in turn, have become risk managers and risk takers in order to provide services to accommodate the company and reduce lost time accidents by reducing personnel. In addition, service providers are educated, insured and licensed to do a job that involves risks like fumigation and confined space entry into hazardous environments. These services are normally performed on holidays, requiring climbing ladders, entering hot and dusty locations, and handling potentially dangerous chemicals.
Pest management is about long-term solutions to pest problems. In the past hundred years it has been convenient to fumigate or spray away a pest problem only to have it come back in days or months. However, the conditions that caused the problem to occur in the first place remain. The survivors begin reproducing to recreate the problem in a short period of time. These conditions still offer an optimum environment and surely will attract more pests from the surrounding area, including outdoors. Again, the long-term solution is to identify and correct the problem and offer the conditions that the insects or other pests cannot survive in. They then will leave or die.
Trends.
A trend has occurred in the last two decades to contract pesticide applications for post-harvest, stored product protection to a select few specialized fumigation and food safety companies. General pest control firms that perform pest management for residential accounts have gotten out of the fumigation business for the most part. The cost of the license, minimum insurance, continued education and capitol cost of new fumigation equipment, including expensive monitoring equipment, has eliminated the small player from this expensive, educationally intensive and potentially high-risk business. Structural fumigations for stored product protection are performed mostly on major holidays and weekends when food plants are closed. In the past, most pest control companies carried fumigation and food-processing licenses, but today only a few very specialized companies exist in North America.
In a continuous quality improvement program, stop to ask: What is causing each and every customer complaint? Is it the vendor who produces a failed package or is it the homeowner that stores his products in infested conditions? Does the package allow the food odor to seep out and be detected by a fertile female Indian meal moth looking for a place to deposit her eggs after it is unsealed? Is a door on the top floor of the food-processing plant left open at night for an employee to keep cool or take a convenient smoke break? Is it the lights placed above the doors attracting light-attractive insects into a food-processing facility? Is it the spiders and their webbing that station themselves near that door to capture and eat the light-attracted insects? Identifying these type of pest issues will lead to a reduction of customer complaints.
This is an excerpt from the book Reducing Customer Complaints in Stored Products by David K. Mueller, BCE.
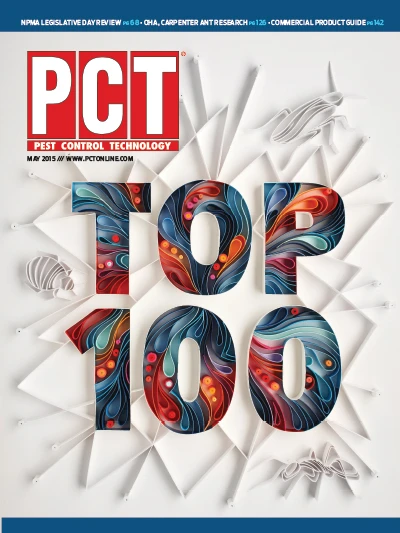
Explore the May 2015 Issue
Check out more from this issue and find your next story to read.
Latest from Pest Control Technology
- Rentokil Terminix Expanded in Key Markets with 2024 Acquisitions
- In Memoriam: Joe Cavender
- Certus Acquires Green Wave Pest Solutions
- Liphatech Adds Alex Blahnik to Technical Team
- Do the Right Sting: Stinging Insect Identification, Management, and Safety
- VAGA's 8th Annual Veterans Thanksgiving Appreciation Dinner
- Clark's Blair Smith on the Response to Increased Dengue Fever Cases in Southern California
- WSDA, USDA Announce Eradication of Northern Giant Hornet from U.S.