![]() |
As the Montreal Protocol continues to reduce and eliminate the use of methyl bromide around the world, various products and processes are being implemented to replace this previously go-to, virtually all-purpose fumigant for control of stored product pests. Two of the non-chemical processes gaining use in Europe, but only gradually getting a foothold in the United States, are heat and controlled atmosphere treatments. (See The Evolution of the Montreal Protocol, at the bottom of this article, for more information on the protocol and methyl bromide.)
At the 10th Fumigants and Pheromones Conference, organized by Insects Limited and Fumigation Service & Supply and attended by 225 people from 33 countries and six continents, discussion of heat and controlled atmosphere were included in the presentations of a number of the global presenters.
The theme of the three-day conference, held in Indianapolis, Ind., in May was “Pest Management Around the World.” It included speakers from Africa, Europe, South America and North America covering a variety of topics from a global pest management perspective, as well as nine hands-on demonstrations.
In the presentation, “How is Europe Surviving Without Methyl Bromide,” Darka Hamel, an entomologist with the Croatian Center for Agriculture Food and Rural Affairs, explained that European scientists began investigating alternatives soon after the 1992 decision that methyl bromide was going to be banned in developed countries as of Jan. 1, 2005. “There was not a common program within the European Union (EU), but scientists have started studies according to their interest, available methods and money,” she said.
Both heat and controlled atmosphere have the advantage of being natural, non-chemical applications that leave no pesticide residual. However, each has its disadvantages as well, including the expense of controlled atmosphere and the limitations of heat on some food applications.
Heat Treatments. Although heat will kill all life stages of insects, there are some advantages and disadvantages to this type of treatment.
What It Is. To kill all stages of food product pests, the temperature in a sealed area or structure is increased to 122°F (50°C) and held for 24 hours or 136°F (58°C) for 16 hours, explained Vasilis Sotiroudas of AgroSpecCom in Thessaloniki, Greece. Of the first method (122°F at 24 hours), Sotiroudas said, “That is the principle accepted around the world as a good temperature and time target.” But, he added, “We have come up with an alternative — we can reach a little higher and be a little shorter because we are killing before 58°C (136°F).”
In trials, Sotiroudas said, the increased temperature has not caused any damage, but it is critical to ensure that the temperature is consistent throughout the area being treated. Although heat treatments can be done by food company personnel, it is necessary to have the proper equipment and understanding of the process, thus, in Europe the treatment is frequently outsourced.
![]() |
There can be extensive variation in temperature from floor to ceiling and wall to wall, depending on duration of heating, building material and equipment in the building, as well as the number of heaters and fans and their placement, said Agriculture and Agri-Food Canada Research Scientist Paul Fields. These factors cause hot and cold spots. “When people start doing heat treatments, often they don’t have enough air circulation. You need lots of powerful fans. Good air circulation can prevent areas from getting too hot, which can damage equipment. Also, it can eliminate cold areas, where insects escape to survive,” Fields said.
Methods and Equipment. Three types of heaters are used for heat treatments, Fields added. These include steam-powered heaters attached to boilers, forced-air heaters using propane or natural gas and electrical heaters. Each has its own advantages and disadvantages. For example, steam has the lowest energy costs, whereas electrical has highest, but it can be better for smaller jobs. Forced-air can be faster than the other methods.
When selecting equipment and method, there is also the question of whether to recycle the air or introduce new air, Sotiroudas said. With air recirculation by electric heaters, it takes about 24 hours to reach 122°F and the temperature must be maintained for an additional 24 hours. With air addition using gas heaters, it takes about eight hours to reach 136°F and maintenance at that temperature for 16 hours.
“Heat treatment is a precise treatment as we are able to monitor every part of the building because we walk in during the treatment,” Sotiroudas said.
The advantages of each method are as follows:
Air recirculation:
- The slower temperature increase provides for better control.
- It is safer near sensitive equipment, such as x-rays, metal detectors, etc.
- Building air currents are more controlled.
Air introduction:
- The quicker temperature increase reduces the treatment time.
- This method is more effective in mill basements and concrete silos.
- It increases pressure so it can penetrate cracks and crevices.
Disadvantages include the following:
Air recirculation
- In buildings with a great deal of concrete, there may be areas where the required temperature is never reached.
- It is very difficult to use for built-in concrete silos.
Air introduction
- The quick temperature increase can damage buildings or equipment.
- It requires closer monitoring.
- Knowledge of gas and increased investment are required.
With the disadvantages of each, he said, there can be an advantage to combining the two methods, targeting basements and cement silos with gas heaters and targeting equipment with electrical heaters.
![]() |
A significant advantage of heat treatments in general is, that because of its non-chemical nature, there are no government regulations controlling its application. In addition, this enables it to be used in a sealed area of a building while work continues in other areas.
When done correctly, the heat is able to penetrate throughout the area or a complete structure, detecting and eliminating pests from hidden areas. However, heat cannot deeply penetrate dense product such as flour, thus enabling pests to burrow down for survival. “This is the reason that flour mills must have no silos or bins full (inside the building) during a heat treatment,” Sotiroudas said, explaining that a small amount of flour forgotten in a conveyor will be heated and insects will die, but a bin with a large amount would never be heated properly.
Care must be taken to thoroughly inspect the structure and equipment within, and to remove items that could be affected by the heat. If a structure is heated or cooled too quickly or the temperature is allowed to rise too high, there is the potential to damage the structure/equipment.
Determining Efficacy. Proving the efficacy of a heat treatment became a challenge, Sotiroudas said, because there were no studies or data from Greek universities. So how does one prove to the customer that the treatment was effective and counter any customer claims that it wasn’t? Sotiroudas recommends that bioassays be used for verification and that this be agreed by the customer prior to treatment. “Mention the survival of bioassays on the contract as the treatment effectiveness decision point,” he said.
The reason this is needed is because, he said, although heat will kill all life stages, there is potential for adults to escape into a structural crack in a window or outer wall, then return after the heat is reduced. To help prevent the survival of these adults, Sotiroudas also recommended that a contact insecticide be applied around doors, windows and cracks. Or, if there is a preference to avoid chemicals, PMPs can use an organic insecticide, such as essential oils, to control any escaping insects.
A Case Study. Nestle Purina PetCare has been using heat since 1993, and today, it is the only treatment the company uses, said Director of Food Safety Kim Kemp. When Kemp joined Purina, he was tasked with developing a new sanitation program. Kemp was interested in pursuing a pesticide-free option. So he began his research focused on the question, “How do you modify your atmosphere to reduce the pest pressure at your plant?” and eventually decided to try heat. In addition to eliminating the pests, Kemp said, “It was the best inspection tool I’ve ever used.”
Initially, he used a self-made portable heater. This transitioned to stationery heaters, and eventually became the process used by all Purina PetCare plants. “Methyl bromide is no longer used or on Purina’s approved list,” he said.
In addition to providing pesticide-free control, the use of heat reduced chemical costs from more than $60,000 pre-heat to $3,000 in 2007 and less than $2,000 in 2011, Kemp said. Today, he added, “Our fogging program is being further modified to be done based only on the insect-catch records for a given area. This will cut chemical usage even further.” The process also gained the company the 2006 EPA Stratospheric Ozone Protection Award.
Controlled Atmosphere. As indicated by the Purina story and the gradually increasing offerings of heat treatment by pest control companies and equipment manufacturers, heat is seeing some use in the United States. However, controlled atmosphere (CA), while becoming more common in Europe, is seeing slower penetration in the United States, which has not yet completely released its hold on methyl bromide critical use exemptions.
What It Is. As defined in a report from the University of California and Getty Conservation Institute, “controlled atmospheres are modified atmospheres that are usually produced artificially and maintained by additionally generating the desired gases (CO2 and N2) or by purging with these gases from pressurized cylinders.”
Replacing the oxygen in the air with carbon dioxide or nitrogen gas kills all stages of insects. The insect’s metabolic process requires oxygen; depriving its body tissues of oxygen causes it to dry out and die.
![]() |
To modify and control the atmosphere of a structure or area to be treated, special equipment processes ambient air, separating out the oxygen and leaving only nitrogen behind. This modified air is pumped into the structure being treated, forcing out the oxygenated air. At the same time, the temperature is increased enough to ensure the insects are active — causing their respiration and metabolism to increase, speeding the time to kill.
According to a paper from the USDA’s Methyl Bromide Alternatives Outreach program, “At exposure concentrations of 0.5 percent O2 for 96 hours, 100 percent mortality has been observed for nearly all insects tested.”
![]() |
However, exact principles of a treatment are dependent on variables such as the product or space being treated, weather and insect being eliminated, Sotiroudas said. Examples he gave included treating bags of sesame for Indian meal moths in the summer with an ambient temperature of 77°F. For complete kill, this insect needs 95°F at one percent oxygen for two days, and one day is needed to reach these parameters, thus a total of three days is needed. But treating bags of rice for rice weevils in the winter with an ambient temperature of 50°F would require three days to reach the needed parameters of 95°F at one percent oxygen for five days, thus a total of eight days is needed.
In addition to the amount of time needed, CA can be expensive, Hamel said. As such, it is used in Europe primarily for smaller consignments and valuable commodities such as spices and herbs, she said, adding that in-bin sealing also is often a limiting factor. CA installations and chambers are present in Belgium, Cyprus, France, Germany, Greece, Italy, Netherlands, Spain, Switzerland and the UK, she said.
Advantages and Disadvantages. The technology can be used in airtight chambers or in silos to treat foodstuffs. Other advantages of CA technology, as detailed by Sotiroudas and Hamel include:
- Being non-chemical, the process leaves no residues.
- There is no danger to workers in the area and no need for an on-site fumigator.
- There is no resistance to controlled atmosphere.
- CA is environmentally friendly and available in many countries.
- Treatments are monitored 24/7 and can be validated with an internationally recognized certificate.
Disadvantages include:
- Cost; investment is required.
- Required duration of treatment may be an issue.
Combining Technologies. While each technology has advantages and disadvantages in and of itself, further options can be provided through the combining of heat, controlled atmosphere and phosphine, Fields said, referencing a technology invented by David Mueller, president of Insects Limited.
The process involves the use of carbon dioxide at three to six percent, heat at 85°F to 105°F and phosphine at 50 to 100 ppm. Sensitive equipment should be removed or sealed. In two trials in Canadian flour mills, the procedure killed 100 percent of adults and 99 percent of eggs of red flour beetles, Fields said.
U.S. Methyl Bromide use. The United States is one of very few countries still using methyl bromide. Having gained permission from the Montreal Protocol for continued critical-use exemptions for 2012, producing and consuming 922.826 metric tons of methyl bromide, the United States is the highest producer/user of the compound. Currently, 93 percent of methyl bromide still in use around the world is used here.
![]() |
In May, the USDA announced a Methyl Bromide Transitions (MBT) program, the goal of which is to “support the discovery and implementation of practical pest management alternatives to methyl bromide uses for which the United States is requesting critical use exemptions.” The program seeks to ensure that economically viable and environmentally sound alternatives to methyl bromide are in place and available as soon as possible for the current 2013 Critical Use Nominations, the announcement stated. The solicitation, which closed in June, focused on integrated commercial- or field-scale research targeting short- to medium-term solutions, associated extension activity to foster adoption and an economic analysis of cost of successfully implementing the transition on a commercial scale.
The author is editor of Quality Assurance and Food Safety magazine, PCT magazine’s sister publication. She can be reached at llupo@giemedia.com.
The Evolution of the Montreal Protocol The Montreal Protocol on Substances that Deplete the Ozone Layer was designed to reduce the production and consumption of ozone-depleting substances to reduce their abundance in the atmosphere, and thereby protect the earth’s ozone layer. Depletion of the ozone layer reduces the shield that protects the Earth from harmful levels of ultraviolet rays. The original Montreal Protocol was agreed on in September 1987 and entered into force on Jan. 1, 1989. Since its implementation, 197 countries have ratified the protocol. Included in the substances whose use was to be reduced, and eventually discontinued altogether, was methyl bromide, an odorless, colorless gas that has been used as a soil and structural fumigant to control pests. Use of methyl bromide was to be completely phased out by Jan. 1, 2005, however, the Montreal Protocol also includes provisions for three broad sets of exemptions, including critical uses of methyl bromide; essential uses for all other controlled chemicals except HCFCs; and laboratory and analytical uses. Additionally, in recognition that methyl bromide use for quarantine and pre-shipment purposes is an important remaining use, the amounts used for quarantine and pre-shipment applications are not included in the calculated levels of consumption and production. However, parties to the protocol are requested to provide information on their national strategies and actions to reduce these uses. According to the most recent release from the United Nations World Meteorological Organization (October 2011), there was an unprecedented stratospheric ozone loss in the Arctic in 2011. The loss was attributed to the continuing presence of ozone-depleting substances in the atmosphere and a very cold winter in the stratosphere. Although adherence to the Montreal Protocol is lowering levels of these substances, the publication notes that, because of the long atmospheric lifetimes of these compounds, it will take several decades before their concentrations are back down to pre-1980 levels, the target agreed in the protocol. The Montreal Protocol also includes a provision enabling parties to respond quickly to new scientific information, agree to accelerate the reductions required on covered chemicals, then automatically apply them to all countries that ratified the protocol. Since its initial adoption, the protocol has been adjusted five times. In addition, the protocol was amended to enable the control of new chemicals and the creation of a financial mechanism to enable developing countries to comply. Unlike adjustments to the protocol, amendments must be ratified by countries before their requirements are applicable to those countries. The U.S. has ratified all amendments.
Source: Compiled from information from the United Nations Environment Program (http://ozone.unep.org) |
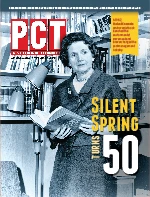
Explore the September 2012 Issue
Check out more from this issue and find your next story to read.
Latest from Pest Control Technology
- Rentokil Terminix Expanded in Key Markets with 2024 Acquisitions
- In Memoriam: Joe Cavender
- Certus Acquires Green Wave Pest Solutions
- Liphatech Adds Alex Blahnik to Technical Team
- Do the Right Sting: Stinging Insect Identification, Management, and Safety
- VAGA's 8th Annual Veterans Thanksgiving Appreciation Dinner
- Clark's Blair Smith on the Response to Increased Dengue Fever Cases in Southern California
- WSDA, USDA Announce Eradication of Northern Giant Hornet from U.S.