Editor’s Note: The 10th Edition of the Mallis Handbook of Pest Control is currently in the process of being completely revised and updated by Editorial Director Stoy Hedges and nearly two dozen contributing editors. We’re pleased to publish the first in a series of excerpts from this eagerly anticipated book in this month’s issue of PCT magazine. The references for this article are available upon request.
Insecticides are rarely available for use in their technical form. The technical grade material must first be mixed or formulated with other components to improve its safety, efficacy, handling, application and storage properties. Components used in mixing or formulating insecticides include carriers, diluents, wetting agents, emulsifiers, solvents and others. Common types of formulations used by professionals include sprayable formulations such as aerosols, emulsifiable concentrates (EC), wettable powders (WP), suspension concentrates (SC), microencapsulated insecticides, oil solution concentrates and ready-to-use sprays. Professionals may also choose from dry formulations like baits, granules and dusts.
The choice of formulation is often as important as the choice of insecticide active ingredient. Before selecting formulations, it is helpful to understand the site(s) to be treated. A complete inspection of the property will provide the information needed to select the best formulation(s) for the job. Carefully consider these 10 questions about formulation selection before making insecticide applications:
1.Can the formulation be applied safely in sensitive areas?
Sensitive areas may include food areas of food-handling establishments, hospital or nursing home rooms, classrooms, certain areas at zoos and numerous other sites. Special precautions must be taken in these areas to avoid potential hazards from insecticide application. First, be sure that the product is labeled for use in these areas. Residual sprays may be limited to crack and crevice treatment and may be prohibited from use when rooms are occupied. Select formulations that are low in odor or have no odor and products with low vapor pressure. Bait formulations are often an excellent choice in sensitive areas.
2. Will the formulation cause phytotoxicity (plant injury) to plants that are treated?
Phytotoxicity may occur following an insecticide application to plants. It is more likely to occur when using liquid formulations like EC formulations that contain solvents. When plants are to be treated, select formulations that do not contain solvents (e.g., wettable powders, suspension concentrates, microencapsulated insecticides). Also, do not treat plants during the hottest parts of the day under direct sunlight. This combination of environmental factors can cause a plant’s foliage to "burn." Other causes of phytotoxicity may be attributed to using excessive rates, treating sensitive plant varieties, cumulative applications to the same plants and mixtures of products. Manufacturers conduct extensive phytotoxicity trials with their products and can usually provide phytotoxicity information. If in doubt, first try the product on a small sample of plants.
3. Is the formulation effective against the target pest?
Regardless of the pest to be controlled, the objective must be to get the insecticide to the pest. Begin with proper pest identification. You should know if the pest is primarily a flying or crawling insect or if it spends most of its time in or below surfaces. Flying pests may be best controlled with a non-residual aerosol formulation. For crawling pests, a residual spray formulation or dust that stays on the surface where pests will contact it may be most appropriate. A bait formulation may be best, especially one that is attractive to the pest and placed in areas where they feed on the bait and ingest a lethal dose of the toxicant. Some active ingredients are selective in their activity against pests, so check the product label to be sure that the pest is listed.
4. Will the formulation perform well on the intended surfaces?
The interaction of residual insecticide formulations and the surface treated greatly affects insecticide performance. Residual insecticides are applied to a wide variety of surface types. These surfaces can be described as porous, semi-porous or non-porous types. Examples of porous surfaces include: concrete, wooden mulches, unfinished wood, gypsum wallboard, paper and plastics. Common nonporous surfaces are glass, ceramic tile and stainless steel. Semi-porous surfaces such as enamel- and latex-painted wood, vinyl tile and Formica will also be encountered.
Numerous studies have shown that EC formulations are absorbed into porous or semi-porous surfaces and the active ingredients are not available to crawling insect pests. Formulations like wettable powders, suspension concentrates, microencapsulated insecticides (CS) and dust formulations are not easily absorbed by porous surfaces and are more readily "picked up" by crawling insect pests. So, if the target pest is a crawling pest, select formulations that stay on the surface. However, if the target pest is found below surfaces (e.g., wood-boring beetles) an EC formulation is recommended. During the inspection and before application, determine which surface types are most common and identify the target pest(s). Once this information is gathered, you will be able to select the most effective formulation(s).
One of the biggest challenges facing the professional is getting cooperation from the customer to maintain good sanitation practices. In the real world of pest management, many of the surfaces treated are coated with oils, grease, food debris, dust or other organic matter, reducing the effectiveness of residual insecticides. Professionals can improve insecticide performance by encouraging their customers to maintain high levels of sanitation.
5. How will environmental factors like temperature, humidity and light affect the formulation?
After insecticides are applied to surfaces, they are subjected to various environmental factors that reduce their effectiveness. High temperatures have been shown to reduce residual effectiveness of chlorinated hydrocarbon and OP insecticides. The effect of humidity on OPs appears to depend on the type of surface treated. Generally, insecticides with higher vapor pressures volatilize (e.g., evaporate away from treated surfaces) more rapidly in the same environments than those with lower vapor pressures. The loss of insecticide residue by volatilization is greatest on non-absorbing surfaces. Vapor pressures are known for each active ingredient and may be obtained by reading the Material Safety Data Sheet (MSDS) provided by pesticide manufacturers. Keep in mind, however, that formulation can affect vapor pressures. For example, microencapsulation protects the active ingredient within a polyurea shell, making the active ingredient practically non-volatile.
Other environmental factors such as ultraviolet light may break down insecticides through photodecomposition. Air currents or wind also can reduce the effectiveness of residual insecticides by increasing the rate of volatilization. The effects of environmental factors can be minimized, especially outdoors, if applications are made to cracks and crevices and other protected areas.
6. Is the product cost effective?
Several factors should be considered when answering this question. First, consider the use rate for the product and then determine the cost of treating a given area (e.g., cost per 1,000 square feet or per home or restaurant). Also, evaluate the time-saving features associated with the use of the product. Savings in labor costs can quickly offset higher insecticide costs. By using this product, can you reduce callback rates? The cost of callbacks is often underestimated. Often, the least expensive product is not the most cost effective.
7. Does the formulation mix easily and can it be tank mixed with other pesticides?
Other than ready-to-use products (e.g., baits, dusts, granules and aerosols), professionals must mix the products they use. Some formulations are easier to mix or handle than others. Liquids like EC, SC and CS formulations are usually preferred over dry formulations such as wettable powders (WP). However, the use of pre-measured, water-soluble packaging for WP formulations has greatly increased the ease in handling this dry formulation.
PMPs should refer to the product label for mixing directions and information about tank mixing. When tank mixing products, follow the most restrictive labeling directions and precautions. Check the label for compatibility with other pesticides. To be sure of physical compatibility, prepare a small sample of the mixture using the proper proportions of water and product.
8. Will the formulation run off or drift during the application?
To reduce runoff or drift of insecticides, monitor the weather and avoid adverse conditions such as heavy rain or high wind. Most runoff of pesticides occurs when pesticides are applied to saturated soils or when heavy rains or excess irrigation occur immediately following application. Under high wind conditions, avoid outside spray treatments. Also, lower spray pressure or use a coarse fan nozzle to reduce drift. When conditions are not favorable for spray applications, use granules. Because granules are generally on a dense carrier, they are not subject to drift. However, when using granules, avoid applications to sidewalks or driveways where rain or irrigation can increase run off. Take care in the placement of applications and avoid broadcast applications when a more targeted application will provide the same level of control.
9. Could there be visible residues on treated surfaces?
Unsightly visible residues on treated surfaces may occur following application of spray treatments. This problem is most common when using WP formulations at high labeled rates and spray volumes. The visible residue is primarily due to the carrier (e.g., talc, clay) used in the WP formulation. Visible residues appear to be more of a problem on indoor surfaces. When applying residuals indoors use EC, SC or CS formulations to minimize the risk of a visible residue.
10. Are there regulatory issues that may limit product use?
ALWAYS READ THE ENTIRE LABEL BEFORE USING A PRODUCT AND FOLLOW ALL LABEL DIRECTIONS. If you are not sure about the use of a certain product, check with local regulatory officials, product manufacturers, distributors or others that can provide clear and accurate information about the product.
It should be apparent that no one formulation will work best for every situation. A professional who consistently uses multiple formulations during a day’s work is taking these questions into account and is more likely to achieve effective results. Take time to inspect and gather important information about the site before making applications.
*****
Extending The Life
Of Your AI —
Not Your Pest
When it comes to pest control, most consumers want their pest management professional to deliver both immediate action and long-term performance. Eliminating pests and keeping them from re-infesting are key considerations for product selection.
BASF helps eliminate callbacks for PMPs with SmartCap Technology and its microencapsulation formulation, enhanced residual control and durability on porous surfaces.
"SmartCap Technology is an important weapon in the PMPs arsenal," said Nick Tresslar, GIC marketing manager for BASF Pest Control Solutions. "Because of the increased residual life of these products, PMPs can reduce their number of callbacks and are able to treat less frequently for the same level of control."
The millions of microscopic capsules in SmartCap products are designed to deliver effective doses directly to pests. Each capsule is composed of a carbon-based polymer shell that holds the active ingredient within a droplet of oil. When a pest comes in contact and breaks a micro-capsule, the active ingredient is quickly released onto the exoskeleton and penetrates quickly because of the oil/waxy composition. Also, because the micro-capsules are smaller than 20 microns, pests can also easily ingest them, BASF reports.
The polymer shell’s solid design allows it to remain intact on surfaces such as concrete or brick, and reduces adsorption onto organic matter, such as landscaping mulch. The polymer shell also helps limit PMPs’ exposure to active ingredients, potentially reducing adverse skin sensation.
BASF offers SmartCap Technologies in multiple products, including Cy-Kick CS, CyhaloCap CS, PermaCap CS and Pyrethrum-based Microcare 3% CS.
To learn more about SmartCap Technology from BASF, visit pestcontrol.basf.us.
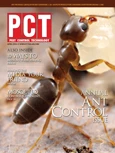
Explore the April 2010 Issue
Check out more from this issue and find your next story to read.
Latest from Pest Control Technology
- In Memoriam: Joe Cavender
- Liphatech Adds Alex Blahnik to Technical Team
- Do the Right Sting: Stinging Insect Identification, Management, and Safety
- VAGA's 8th Annual Veterans Thanksgiving Appreciation Dinner
- Clark's Blair Smith on the Response to Increased Dengue Fever Cases in Southern California
- WSDA, USDA Announce Eradication of Northern Giant Hornet from U.S.
- Ned’s Home Acquires Ultra Safe Pest Management
- Bed Bugs & Dirty Clothes