Purchasing has been an incredibly difficult road over the past couple of years. We should have known the path we were heading down when lines and limits began to form for everyday items such as toilet paper. Today, we are seeing supply chain issues for chemicals, equipment, materials used for packaging and applying our products, vehicles, personal protective equipment and even shipping itself.
While you are concerned about forecasting your potential needs, have you thought about how this affects your training program? We can’t afford to overuse any of our products or let our equipment fail. Here are a few tips to consider this year while building and presenting your training.
PPE USE AND COMMUNICATION. As these items became more and more limited, not wearing them was just not an option. We had to make sure our staff and valued teammates understood what we were doing behind the scenes to make sure they had the items needed to perform their job functions safely. That is our OSHA responsibility, after all. We had to make sure that we trained on notification procedures when these items were running low.
The communication between field employees and managers must be at a higher level to ensure they always stay stocked with equipment. Teammates couldn’t rely on simply running into their branch office if they ran out of gloves or needed to replace their respirator cartridges. We had to train on proper life expectancy on our most-needed PPE items.
When should you notify your manager when you’re running out? Expected order delays and option limitations put more weight on having more time to restock equipment. This put a stress on proper communication ahead of time. When you start to notice small issues or defects in your equipment, bring it up then.
PROPER APPLICATIONS. Making a proper application has always been a core training function within the pest control industry. Now, we add in the challenges of getting products and put an even bigger emphasis on proper product usage.
Proper application training starts with a thorough label review. Does the employee know how to mix the product for various applications? Do they know what those different applications are? Do they know the application rate? These are basic math skills that often go untrained.
Now that we know how much product to mix, we need to be able to select the appropriate equipment and calibrate it. Proper calibration can determine the fine line of proper application versus overapplying or even underapplying the product.

A couple of examples include marking off a 1,000-square-foot area and having technicians time themselves treating this zone or performing a bucket check on a spray rig. Even our granular applications must be calibrated.
NEW PRODUCTS. You just got word back that your favorite go-to product is unavailable or is on backorder. To make the transition as smooth as possible for your employees, try and select products that are very compatible. For example, if the prior aerosol product was labeled for drains and you replace it with one that is not, you are liable to have a couple misapplications from your field staff who may miss this difference. You should always completely review a product before adding it to your company’s approved materials list.
Next, before this product ever hits your employees’ vehicles, you should ensure that they are properly trained on all facets of the new product. Describe why you chose this product to replace the original on your approved list. Show them where they can pull up the product label and SDS sheet. Walk through the entire label and answer any questions that your team might have. What PPE should they wear? Where can this product be applied? Does that differ from the old product they used? Is it labeled for the same target pest? Is the mix rate the same or different? All of these are great points that should be reviewed.
I like to conduct this training by pulling up the label, either digitally or printed, and having various employees read through each section and discuss the answers to these questions aloud. Make this a routine. Build a monthly rotation of product labels that your team reviews. I promise, even a 10-year veteran who has treated thousands of homes with a product might still pick up something new on the product label. Teach them how to properly read a label so they can adapt their learning to any product you hand them.
EQUIPMENT USE AND MAINTENANCE. Equipment can be hard to come by and replace, so proper care and maintenance is extremely important to prolonging its service life. Start by training on the proper use of the equipment. Demonstrate the appropriate ways to use the equipment and show examples of what happens when you don’t take care of it. It can be especially beneficial to show spray tips that have been damaged due to abnormal wear and tear.
Poorly maintained equipment will affect your product usage. Create maintenance schedules for your pieces of equipment. How often should a handheld sprayer be cleaned? How often should you clean your filters or change the oil on a pony motor? What are some basic field maintenance steps that they can take to troubleshoot an issue?
Save old parts and worn-down equipment to use for show and tell. This helps the employee see what could happen if parts aren’t properly maintained.
One piece of equipment that we often forget to train on, which is one of our largest pieces of equipment, is the service vehicle. We know that proper maintenance and taking care of our vehicles will prolong their service lives. Ensure that your team knows how often to get an oil change, how to check their tread depth and when to notice brakes going bad. We want our drivers to take ownership of their service vehicles. Again, use photos of damaged vehicles, worn tires, bad brakes, old oil, bad wipers, etc., to drive the topic of discussion.
FINAL THOUGHTS. Overall, we must be able to adapt and react to our ever-changing environment. We are such a resilient industry, and we need to take that mentality to our training programs. How can you change up your hands-on training to meet the needs of backordered products, shortages of vehicles and equipment, etc.? By training on communication, proper applications, new products and proper equipment maintenance, you can ensure your team is ready to meet the needs of 2022.
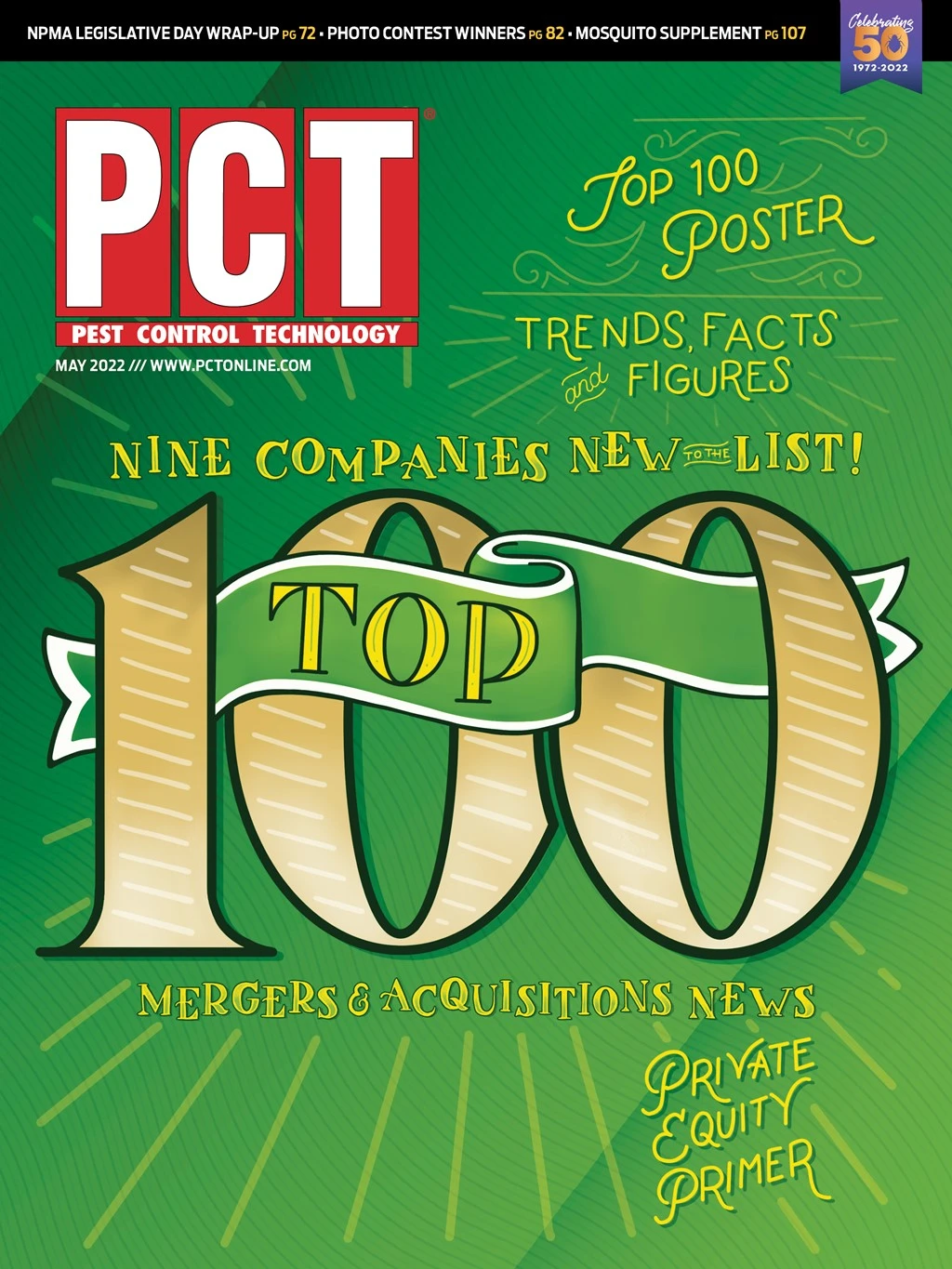
Explore the May 2022 Issue
Check out more from this issue and find your next story to read.
Latest from Pest Control Technology
- In Memoriam: Joe Cavender
- Liphatech Adds Alex Blahnik to Technical Team
- Do the Right Sting: Stinging Insect Identification, Management, and Safety
- VAGA's 8th Annual Veterans Thanksgiving Appreciation Dinner
- Clark's Blair Smith on the Response to Increased Dengue Fever Cases in Southern California
- WSDA, USDA Announce Eradication of Northern Giant Hornet from U.S.
- Ned’s Home Acquires Ultra Safe Pest Management
- Bed Bugs & Dirty Clothes