
Hand-held compression sprayers (HHCS) have been a standard piece of equipment for PMPs for more than 50 years. And battery technology has accelerated innovations in the design and utility of this iconic symbol of the professional pest management industry. Yet, the last study that investigated the effects of pressure, nozzle tip and walking speed on output and deposition patterns from hand-held compression sprayers was in 1973.
It is well documented that the amount of material applied using an HHCS (spray volume) is influenced by pressure (magnitude and consistency) as well as the nozzle tip. The most common tips used by PMPs are flat fan (800067), cone and pin stream (adjustable 5500 ConeJet). In 1973, Rogers, Roth and Price concluded that an 800067 fan nozzle tip (8.57 ounces per minute at 40 psi) provided the least amount of drift at pressures between 10 to 20 psi with a walking speed of 2.5 feet per second (an average technician’s walking speed). The other tip they tested, 8002 fan nozzle (25.6 ounces per minute at 40 psi), provided the least amount of drift with lower pressure (5 psi) and faster walking speed (5 feet per second).
The researchers’ definition of how to attain spray patterns that provided the least amount of drift highlights the need for a technician to understand that pressure and tip are the main factors that influence how fast they can walk to deliver a label directed volume of product. There are other influences on the distribution of product that comes out of the nozzle, such as wind speed/direction as well as spray angle and distance from the target. However, the applicator has influence over two important factors (pressure and tip) that are essential parts of the process of calibrating an HHCS, which is the only way to know if your application is over or under the label directions.
Manufacturer technical factsheets can be difficult to interpret and apply to situations encountered by technicians in the field. Equipment calibration is required training for registration as a PMP in many states, as well as lessons involving pesticide safety. However, a search of web links offering lessons in calibrating HHCSs showed that 100 percent of them were best suited to agricultural or lawn care use patterns. Time in which volume is acquired is an important component in calibration and the average for the five randomly selected web links was 65 seconds. The choice of nozzle tip, pressure and time affect the calibration process, which in turn impacts volume applied, and therefore spray coverage from HHCS.
Our goal was to examine spray coverage using HHCS and our efforts demonstrated the importance of knowing your equipment. The often-overlooked impact of pressure and the selection of nozzle tip was highlighted and, in turn, demonstrated the need for calibration toward understanding the coverage provided when applying pesticides using HHCS. Lastly, we illuminate the coverage provided when using an HHCS under a single-pass exterior perimeter label application.
MATERIALS/METHODS. There were two parts to our research: testing the equipment and simulation of the coverage provided in an exterior perimeter treatment.
Part A: Sprayer output and pressure. Three commercially available HHCSs were used (Table 1). A Norgren gauge, port size 1/8-inch was installed at the tank and control valve of each sprayer (Photo 1). The sprayers also had a Norgren regulator, RO7, port size 1/8-inch, installed at the control valve (Photo 1). Sprayers were filled with water (Table 1) to the full tank mark. The regulator adjustment was turned counterclockwise to initially remove force on the regulating spring and then in a clockwise direction while pressurizing the sprayers. All sprayers were pressurized by hand pump to 18 psi and two sprayers (sprayer #2 and sprayer #3) also were pressurized using their respective battery/electric assisted pumps. We sprayed into 100-, 500- and 3500-milliliter graduated cylinders for 6, 30 and 60 seconds, respectively, and then recorded the volume of spray (milliliters) as well as pressure gauge readings at the tank and control valve.
Part A: Nozzle tips. Four nozzle tips were tested with all sprayers: 5500-X8 adjustable ConeJet brass tip full cone (setting A) with 66° spray angle, 5800-CC 4-way tip coarse fan (#50015) at 50°, extended range (XR) 11008 stainless steel (VS) coarse flat spray at 110° and XR11008 ceramic (VK) coarse flat spray at 110° (Table 2). There were five replications for each of the 12 sprayer/nozzle combinations.
Part A: Procedures to calculate the required treatment time and walking speed. An insecticide label’s application rate of 1.5 gallons per 1,000 square feet was used to calculate that 681 milliliters (23 ounces) of product is required to treat 1 foot up and 1 foot out along a 60-linear-foot foundation. That assumption translates to 60 x 2 linear feet or 120 square feet to compare to the label instructions (Photo 2). We calculated the required time to treat 120 square feet using the volumes obtained from the 6-, 30- and 60-second calibration exercise. Finally, walking speeds were calculated to apply label volumes 1 foot up and 1 foot out along 60 linear feet of foundation (see box for sample calculations.)


Part A: Actual output in determined required treatment time. Spray volume (milliliters), as well as pressure gauge readings at the tank and control valve, were recorded for the three sprayers with each of the four nozzles with and without pump-assisted pressures. We then compared actual output volume collected in the time required to make a label directed application to a 60-linear-foot foundation with the expected value of 23 ounces (Table 6).
Simulation of the coverage provided in an exterior perimeter treatment. Three HHCSs equipped with gauges were used, as described in Part A. Vision Pink (GarrCo products, Converse, Ind.) dye solution (1 to 3 percent) was sprayed onto Kromekote indicator cards (CITI Paper USA) along the foundation of a wall on the University of Georgia campus (Photo 3). Sprayers were calibrated to provide the 1-foot by 1-foot label-directed coverage with a single pass, using a device (Photo 4) that held the nozzle tip of each sprayer at a uniform distance and consistent angle from the foundation. Sprayer 1 was pressurized by hand pump and two sprayers (sprayer #2 and sprayer #3) were used with their pump-assisted pressures.

Three nozzle tips were used: 5500-X8 adjustable ConeJet brass tip full cone (setting A) with a 66° spray angle, 5800-CC 4-way tip coarse fan (#50015) at 50° and XR8005VS coarse flat spray at 80°.
The previously calculated walking speeds were maintained using a metronome app for Android devices (The Accountancy Partnership, London). The coverage along the foundation was measured using five sets of four Kromekote cards placed at intervals along the junction of the foundation and wall (Photo 3) and pressure was monitored using the installed gauge. There were five replications for nine sprayer/nozzle pairs. Indicator cards were analyzed by measuring the length of Kromekote cards fully covered with dye solution (full coverage) and the distribution of dye above and below the treatment area (off-target coverage). A total of 532 cards were scanned and analyzed using Deposit Scan software and percent coverage was recorded for 4 inches above and 4 inches below the label-specified 24-inch treatment zone.
RESULTS. Regarding the effect of pressure, nozzle and time on spray output, sprayers starting with an operating pressure of 18 psi steadily lost pressure over time when the control valve was open, and that pressure drop provided reduced spray volume over time (Table 3). This means that if you use a six-second output calibration but don’t pump your sprayer as you conduct a treatment that takes three minutes, the actual output will be far less than expected. However, when sprayers were used with pump assisted pressures, they provided closer to expected volumes because there was less pressure drop over time.

Nozzle selection also influenced spray volume across sprayers and pressures. We categorized extended range tips (XR) as High Output (HO) because flow rates at 18 psi were three times greater within the same time interval, compared to the 5500-X8 ConeJet full cone and 5800-CC 4-way coarse fan that we termed Low Output (LO) tips. Tank pressure fell faster and farther with the HO tips.
Treatment time and walk speeds are important factors. The calculated time-to-treat 60 linear feet using calibration volumes obtained in the 6 second calibration time resulted in walking speeds that were less than 1 foot per second with LO tips; a maximum of 0.5 foot per second for sprayer 1 and sprayer 2 used with low pressure and a maximum of 0.7 foot per second with higher pressure (Table 4). The walking speeds for 60 linear feet were all greater than 1 foot per second using HO tips regardless of the pressure. Spray output values with all HO tips, including the XR 8005, resulted in walking speeds that completed a 30-linear-foot perimeter in under 30 seconds regardless of the pressure; more than one minute using LO tips with low pressure; and with higher pressure, the speed was less than one minute. (Visit www.pctonlinecom and click on “online extras” to see videos.)
Actual output in the required treatment time vs. expected output varied. We used a one-tailed t-test to compare mean output (n=5) by sprayer and nozzle with the expected label-directed volume of 681 ml. All spray volumes were significantly different from the expected except two, while the range of mean spray volumes varied from 14 percent less than expected (583 ml) to 17 percent greater than the expected (795 ml) (Table 6). There was an unexpected amount of variability in these data although the range of values for a specific sprayer/tip combination showed most were consistently over or under the expected volume with either the 6- or 60-second calibration time. There was a trend with Sprayer 1 (low pressure no assist in maintaining pressure) with the LO tips providing consistently below expected volumes; with the HO tips the 6-second volumes were below and the 60-second volumes above expected which highlights the importance of maintaining pressure. Sprayer 2 (low pressure with pressure assist) provided above expected with the 5500-X8 ConeJet tip for both calibration times; below expected with the 6-second time but on the mark with the 60-second time using the 5800-CC 4-way tip, while the HO tips provided below expected at 6 seconds and above expected with the 60 second calibration time. Sprayer 3 (higher pressure with pressure assist) provided below expected with the 5500-X8 ConeJet tip and above expected with the 5800-CC 4-way tip using both calibration times, below with the VS tip at 6-second but on the mark with the 60-second calibration time while it was below expected with both calibration times using the VK tip (Table 6).

We simulated the coverage that a PMP would provide in an exterior perimeter treatment. Full coverage was defined as the length (inches) of cards fully covered with dye solution (Photo 5).
All sprayer/nozzle combinations provided on average, full coverage (n=45) of at least 22 inches in one pass along 30 feet of foundation. The only sprayer/nozzle combination that resulted in over 24 inches of full coverage was sprayer 3 (high pressure with pressure assist) with the XR 8005 VS HO tip (Table 5). Off-target coverage was defined as the proportion of an area that had dye 4 inches above and 4 inches below the label-specified 24-inch treatment zone.

There was variability in off-target percent coverage with all sprayer/nozzle combinations (range of median percentages varied from 0 percent to 60.6 percent coverage) but two trends were evident. The 5500X8 ConeJet tip had the most variability and higher percent coverage than the 5800-CC 4-way nozzle with all sprayers. Additionally, the use of sprayer 3 at high pressure increased off-target percent coverage with each tip. Sprayer 2 (low pressure with pressure assist) with the XR8005 VS HO tip provided the least off-target percent coverage and variability in off-target spray (0 percent-3.3 percent).

DISCUSSION. Calibration ensures that the proper amount of product is applied and pressure and nozzle selection impact spray volume. The output from any nozzle/sprayer combination will be less over time as pressure drops in the sprayer, and consistent pressure is a driving force in maintaining predictable sprayer output. When sprayers use a battery/electrical pump assist, the pressure is more consistent (dropping only 1-2 psi in our tests using LO tips with the control valve open for more than 1 minute). There are several advantages to using pump-assisted pressures, compared to equipment where the technician must stop, periodically, to pump up the sprayer. HO tips have a higher flow rate and therefore spray more liquid than LO tips in the same time interval causing greater pressure loss over time resulting in the application of more product than expected by calibration (if the calculated treatment time is shorter than the calibration time).
Our data on actual output in the time required to treat 60 feet of foundation in one pass vs. expected output showed consistent predictability with various sprayer/nozzle combinations highlighting the importance of knowing your equipment (Table 6). The variability we recorded when calibrating HHCSs ranged from -14 percent to +17 percent error in actual output. Anticipating that type of potential error demands that calibrations be conducted to ensure you are doing everything possible to reduce over or under application of product on a job. Spray volumes undoubtedly vary when pressure is inconsistent, especially when pressure falls during calibration resulting in predictable overapplication. The largest deviation from the expected that we recorded (17 percent more than expected) was using the 60-second calibration time with sprayer 2 and the XR11008 VS tip. That amount of overapplication translates to applying 13 extra ounces over a 200-linear-foot treatment area (for a 2,400 square foot single-family home). The point is that a small error in calibration can, using the current example, mean overapplication of 130 ounces during a 10-house route. It is also likely you could sacrifice efficacy with an under-application estimate as with sprayer 2 and XR11008 VS tip, using a 6-second calibration time (Table 6). That translates into 11 fewer ounces than on the product label per 200 linear feet in the example mentioned earlier. Applying less product than specified by the label may impact the level of control achieved with that treatment. However, applying more product results in added cost, not to mention potential negative environmental or regulatory impacts (it is against the law).

We recommend calibrating by making one pass with the sprayer and estimating walking speed to ensure the label-directed amount of product. Too little product could impact efficacy. If the estimated walking speed is too slow, one might go around a building in two trips. Sweeping the tip multiple times while walking would not be easily calculated and would probably not provide consistent coverage. It is possible to deliver the correct amount and keep within the label-recommended coverage in one single pass with an HHCS. Our coverage data showed that both the magnitude of pressure and nozzle selection influenced the probability of spraying outside the intended treatment area, which, again, underscores the importance of knowing your equipment. Ensure that correct walking speeds are calculated from the calibration process and that the nozzle is held at the correct distance and height from the intended treatment area if you want to, in a single pass, provide the most consistent spray pattern with an HHCS.
Both authors are with the University of Georgia. Williams-Venegas is a recent graduate and Forschler is a professor. Photos are courtesy of the authors.
References cited
Rogers, R., Roth, L., & Price, R. (1973). Spray Patterns and Drift from PCO Hand Sprayers. Pest Control, 24-28.
EPA. Apply pesticides correctly.
Robinson, W. and Patterson, C. 2010. [Technical Report] Making the Right Nozzle Choice. PCT Online. www.pctonline.com/article/pct1009_techreport.
Future of Spraying in Pest Control: Automated Compressed Air Technology Vs. Manual Pump Systems. Green Gorilla White Paper, 2016.
Spraying Systems Co. 2014. TeeJet Technologies Catalog 51A.
Georgia Structural Pest Control Commission (rev. 2015). Employee Registration Manual.
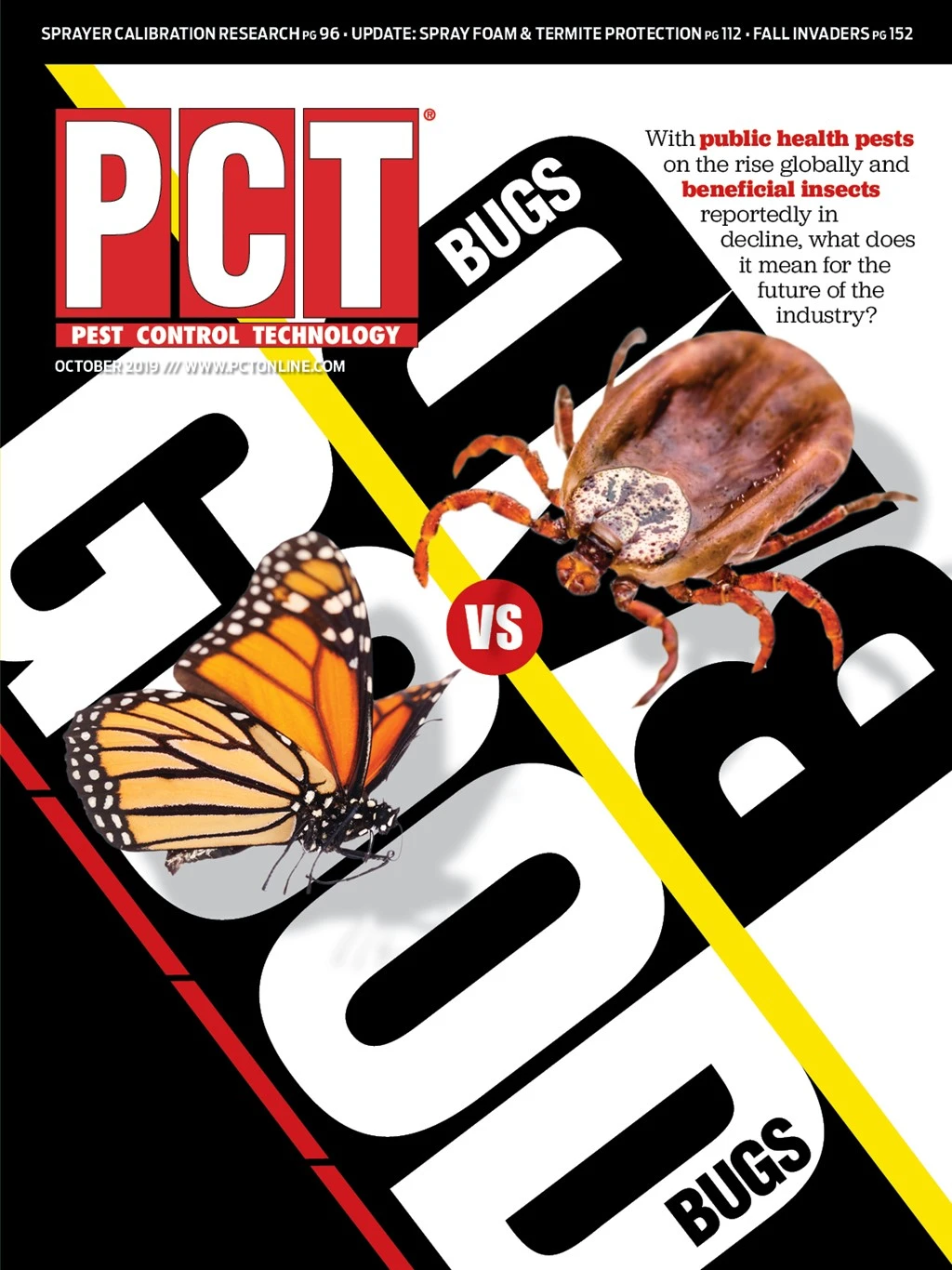
Explore the October 2019 Issue
Check out more from this issue and find your next story to read.
Latest from Pest Control Technology
- Rentokil Terminix Expanded in Key Markets with 2024 Acquisitions
- In Memoriam: Joe Cavender
- Certus Acquires Green Wave Pest Solutions
- Liphatech Adds Alex Blahnik to Technical Team
- Do the Right Sting: Stinging Insect Identification, Management, and Safety
- VAGA's 8th Annual Veterans Thanksgiving Appreciation Dinner
- Clark's Blair Smith on the Response to Increased Dengue Fever Cases in Southern California
- WSDA, USDA Announce Eradication of Northern Giant Hornet from U.S.