When we think of insecticide applications, we all know the label is the law. We typically think that we have to apply a product in a power sprayer rig the same way we would using a backpack sprayer. But there are many situations in which this is not the best method for delivering the product to provide a quality service for the client.
Let’s say you have taken over an account that has had repetitive ant problems for many years. They have mulch that is 8 inches thick, has been there for a number of years and has never been replaced. This customer has no interest in spending the time or money to get rid of this mulch, but now you own the ant problem. If you take the standard approach to a liquid application, you will have the same results as the previous company. If you use a high-volume application, you will increase the likelihood of elimination and win over the customer, creating a raving fan.
THE DETAILS. The first thing you have to think about is the rate difference. Let’s say you normally use a product that has a mix rate of 0.27 fl oz/1,000 sq ft in 1 gallon of water. Since we have to get the product through the multiple layers of mulch, we have to use more water. We use the same 0.27 fl oz of product, but this time, we dilute it with 5 gallons of water/1,000 sq ft. Since the label says we can apply 0.27 fl oz of product/1,000 sq ft, the volume of water does not matter. What ends up happening is we reduce the concentration from 0.075% to 0.015% while delivering the proper amount of product to the client for their service. Even though we have diluted the active ingredient further, it allows us to get a better spread of the product through the substrate. This type of product delivery can have better results if you rake the mulch to allow for better saturation as well.
The next part is to ensure that your equipment is calibrated properly for volume output. The question you have to ask yourself is how many gallons per minute does your rig put out? There is a big difference between 2 gallons/minute and 3 gallons/minute. Think about your rig, and then go test it.
A simple way to calibrate your set up is to take a 5-gallon bucket, time how long it takes to fill up, and then do some simple math to find out what volume your equipment is pumping out. The items that can affect your calibration are the engine speed, pressure setting, the age of your equipment and hoses, and the type of tip you are using. If any of these change, then your calibration is going to be off. If you are performing a highvolume application, you need to ensure your equipment is calibrated properly or you can perform a label violation and/or waste money by applying too much product. You could also be setting yourself up for callbacks and having an unsatisfied customer by applying too little product. I usually recommend people calibrate their equipment weekly to ensure accurate application rates.
After you know what your equipment is pushing out, you have to know what individual application technique you will use. To do this, you will need to set up a test plot and figure out how much liquid you use in that test plot. You measure out a precise amount of liquid and spray it on the test plot. If you use a 50- x 20-foot (1,000 square feet) test plot and spray 2 gallons of water over it, then you can look at the label rate to determine how much product you need to add to properly service the account. If you change anything on your rig, then it will most likely need to be recalibrated.
FINAL THOUGHTS. Knowing how to calibrate your equipment is important for applying any product, whether it is for a high-volume application or not. However, the stakes get raised when you start diluting the product further than the standard fluid ounces/1 gallon mixture. Learning what your equipment and individual application rates are will help you apply the product properly.
Now that we know what our equipment is calibrated at, and we know our individual application technique, we can take care of our customer properly. Even though that mulch is really thick, we can now apply a treatment that will allow us to penetrate through the mulch and eliminate the ants. Now we can see how using a high-volume application will allow us more flexibility to resolve our customers’ pest issues.
David Moore is a board certified entomologist who received his master’s degree in entomology from Virginia Tech. He serves as the manager of technical services for Dodson Bros. Exterminating. Contact him at dmoore@gie.net.
Copesan is an alliance of pest management companies with locations throughout North America. To learn more, visit www.copesan.com.
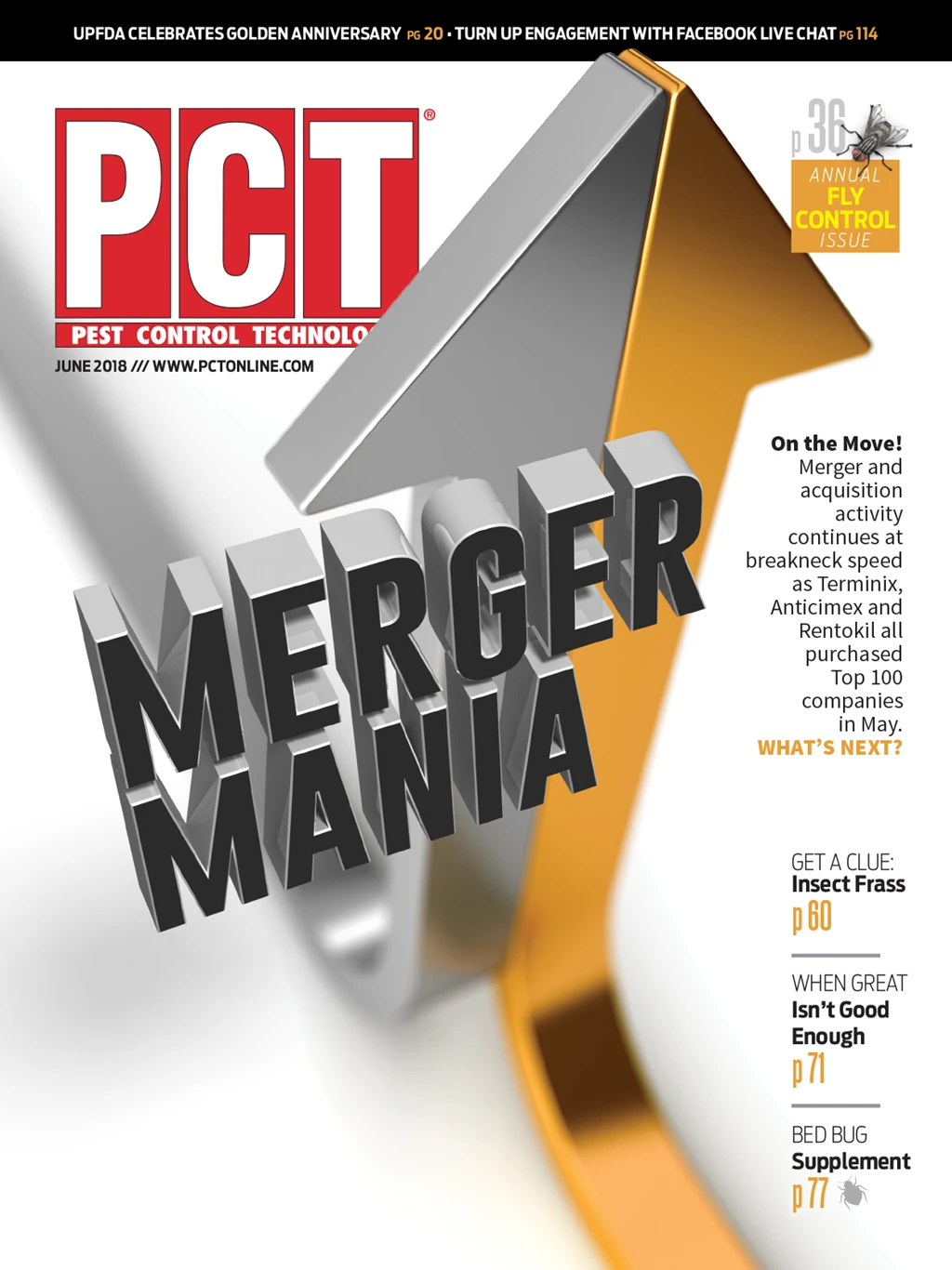
Explore the June 2018 Issue
Check out more from this issue and find your next story to read.
Latest from Pest Control Technology
- Liphatech Adds Alex Blahnik to Technical Team
- Do the Right Sting: Stinging Insect Identification, Management, and Safety
- VAGA's 8th Annual Veterans Thanksgiving Appreciation Dinner
- Clark's Blair Smith on the Response to Increased Dengue Fever Cases in Southern California
- WSDA, USDA Announce Eradication of Northern Giant Hornet from U.S.
- Ned’s Home Acquires Ultra Safe Pest Management
- Bed Bugs & Dirty Clothes
- Boston Adopts Liphatech's IGI CO₂ Technology for Rodent Abatement